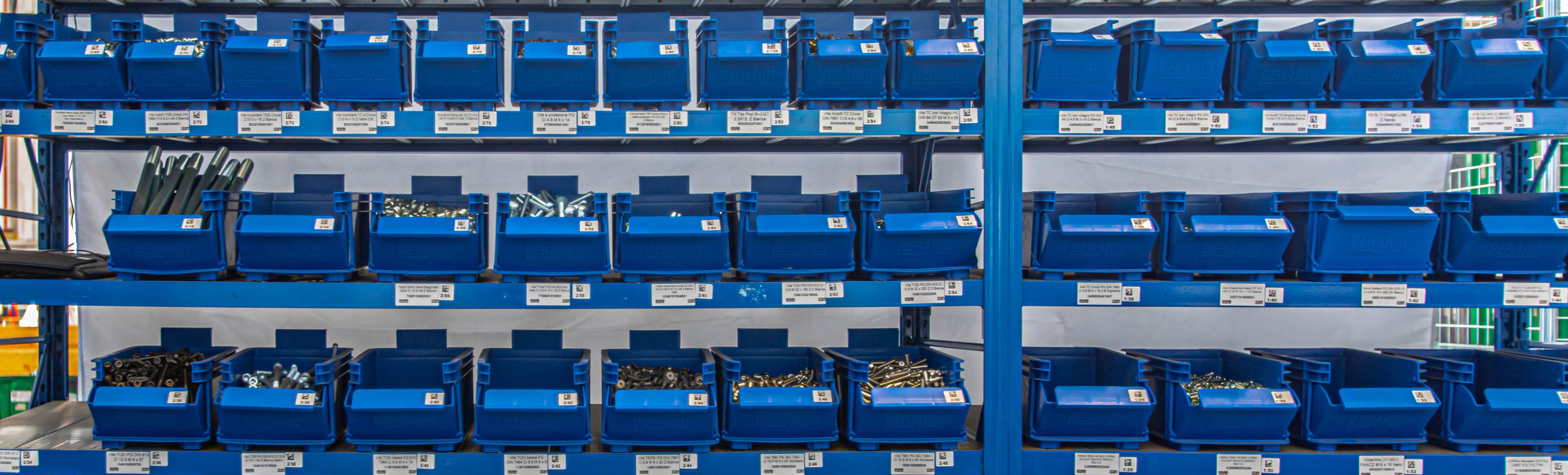
Reduce warehouse management costs
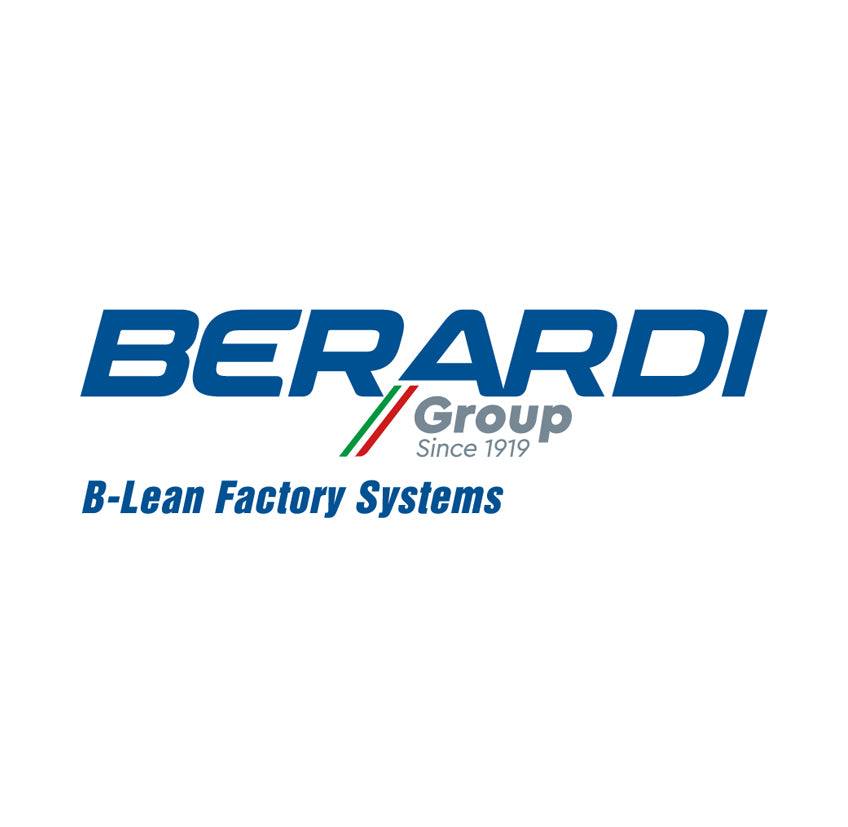
B-Lean Factory Systems
New logistics division of Berardi Group
Berardi, on the fastener world scene for over 100 years, inaugurated 2021 by enhancing its logistics division by launching "B-Lean Factory Systems". A competent team, specialized in the development and design of logistics solutions, which offers expertise and consultancy to customers, analyzing individual needs and process phases to be improved, both in terms of complexity of solutions and flexibility and speed of response. The new division follows the mission of Berardi Group: to give customers a 360° service, eliminating all waste and making them forget about the management of class C elements and industrial components used in the assembly of the finished product.
A personalized service
An integrated logistics service, tailor-made to the customer's needs
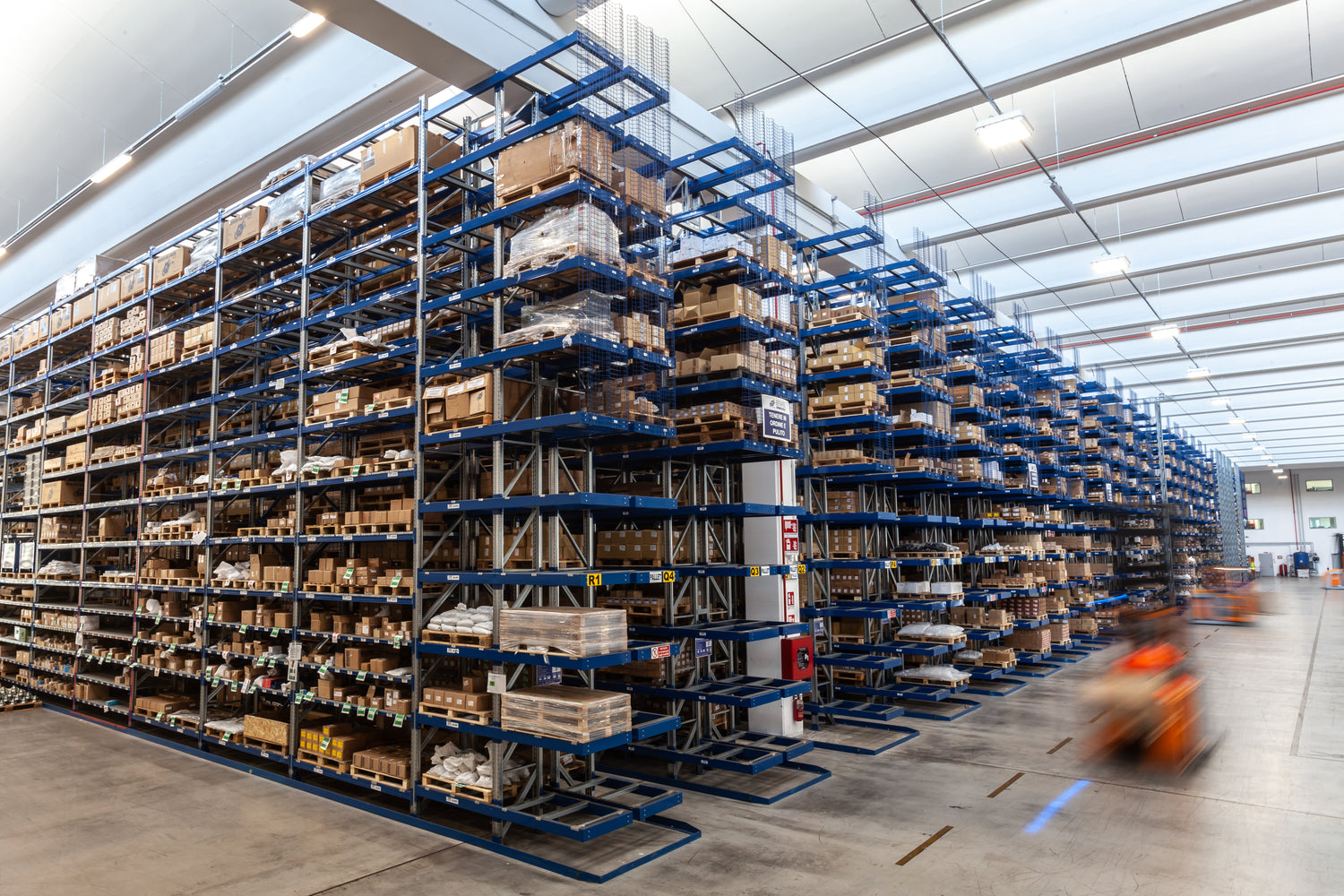
Integrated Logistics
Experience teaches us that logistics efficiency is the starting point to identify and best satisfy the needs of each customer. The Berardi Bullonerie headquarters with the Technical, Quality, Kanban and Purchasing departments is supported by a multi-warehouse system that guarantees efficiency, flexibility and proximity to the customer with a widespread and personalized service.
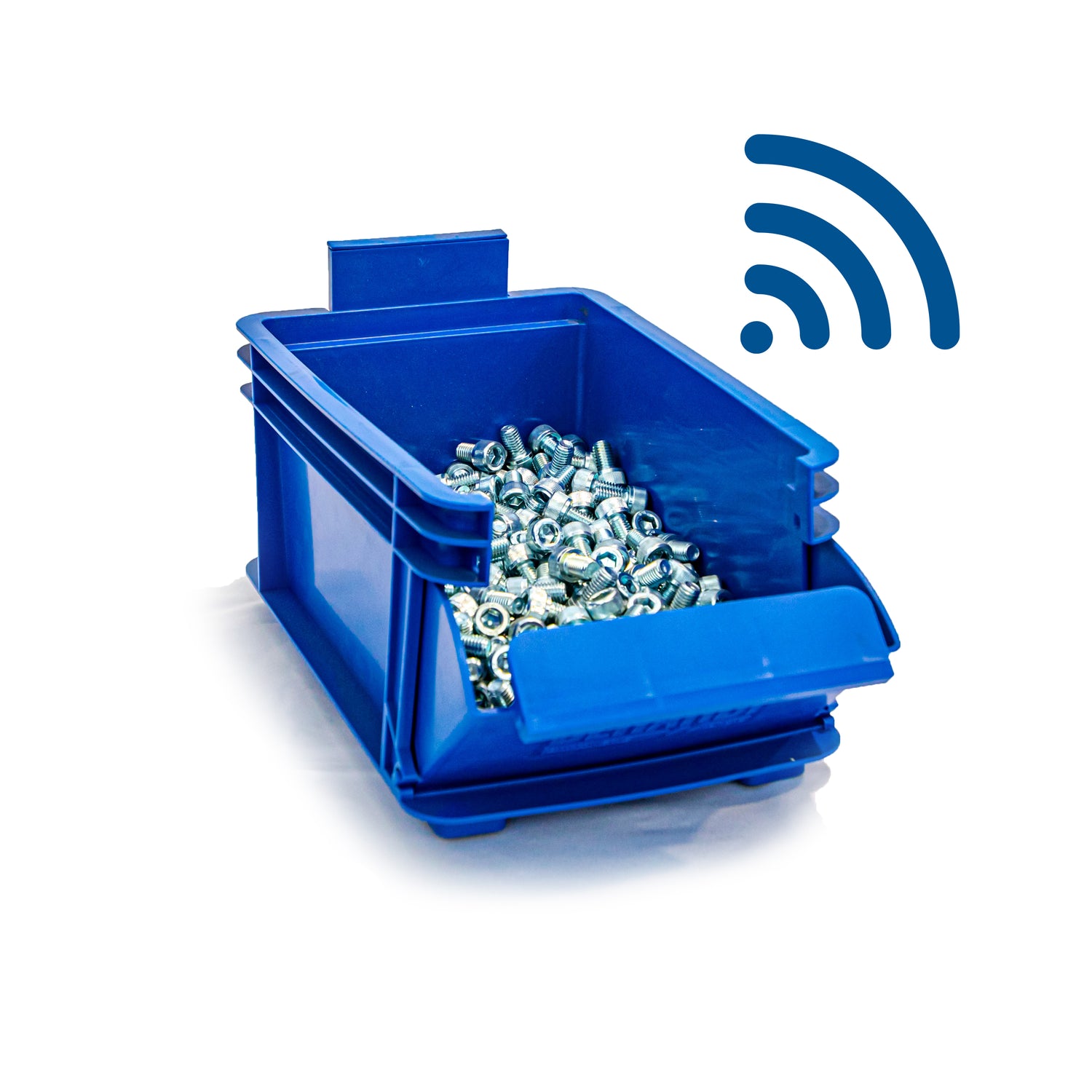
S-BBK: the new system by Berardi Bullonerie
S-BBK 4.0 is a highly technological Smart container, equipped with capacitive intelligence and integrated electronics thanks to which it constantly communicates the quantity of material contained, thus allowing you to know the status of the Stock at any time and to automate supply activities. When the quantity inside the container is equal to or less than the pre-established Reorder Point, the system automatically generates a refilling request, which is sent on a regular basis, on the planned fulfillment days.
Are you already a Kanban customer?
Access the KanbanUp portal to manage your orders quickly and easily.
Take back your time!
Thanks to integrated logistics services, you minimize waste: you save time and
the resources employed in the management of low value-added activities.
The benefits for your business
-
Logistics consultancy
-
Quick orders
-
Custom packaging
-
Logistics flow traceability
-
Reduction of supply chain costs
-
Reduction of circular capital
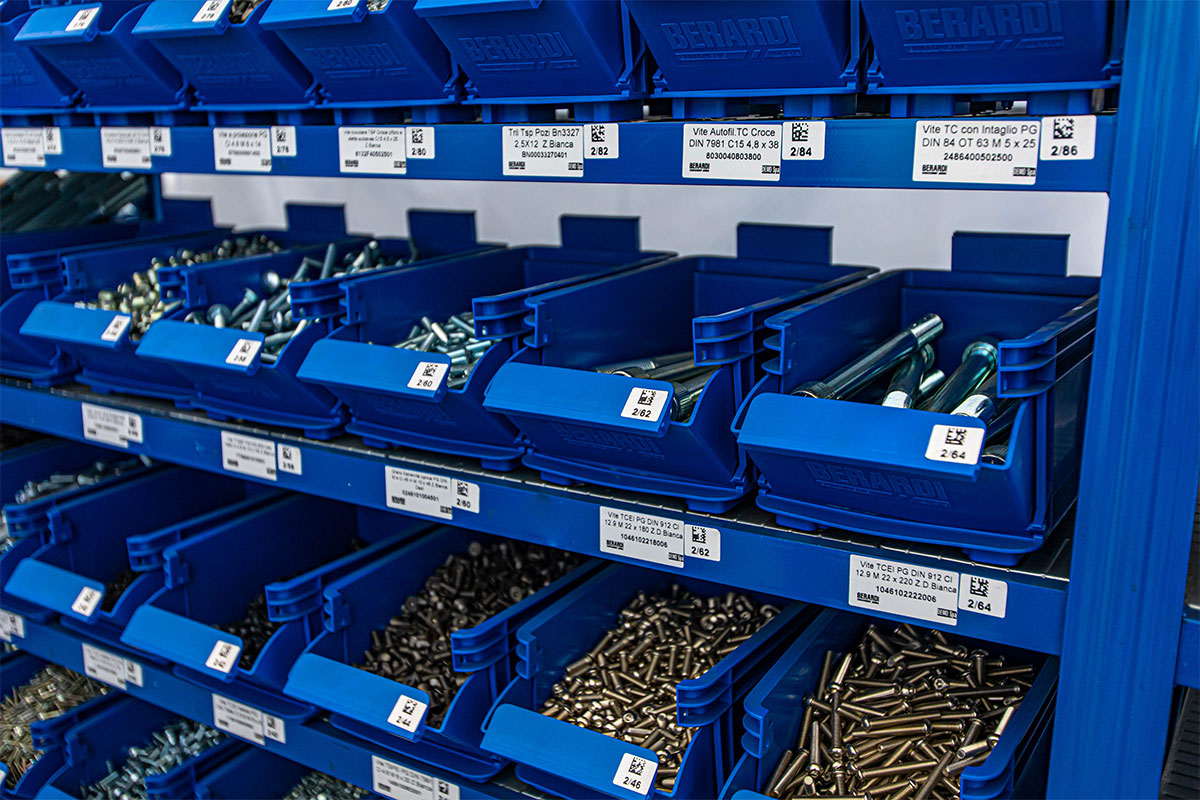
Reduce costs with Kanban service
Our Kanban is a just-in-time supply system that allows you to outsource the management of small metal parts and all items catalogued in class C and to allocate valuable internal human resources to activities with greater added value. Customers with our Kanban service receive the material directly in the production supermarkets or on the assembly line. The cadence and quantity of orders are pre-established during the design phase of the service.
The B_Lean Factory Systems Team, with the experience of over 500 active Kanban systems, can support the customer in the service design phase , offering efficient and customized solutions to reduce waste and improve supply flows , reducing costs and resources involved in the management of class C items.
The Benefits of Kanban
-
Logistics and production
Reduction of stock levels
Elimination of out-of -stocks
Less space occupied by the warehouse
Reduction of handling times and costs
Greater order and cleanliness
Internal resources freed up from logistics management
Traceable consumption and usage statistics
-
For the purchasing office
Reduction analysis of needs
Reduction of requests for quotations
Deleting purchase orders
Reminders elimination
Resources freed up by C-Class Material Purchasing Management
Fewer suppliers to manage
Electronic DDT : load incoming material and download the purchase order, automatically
Direct monitoring of consumption of external productions
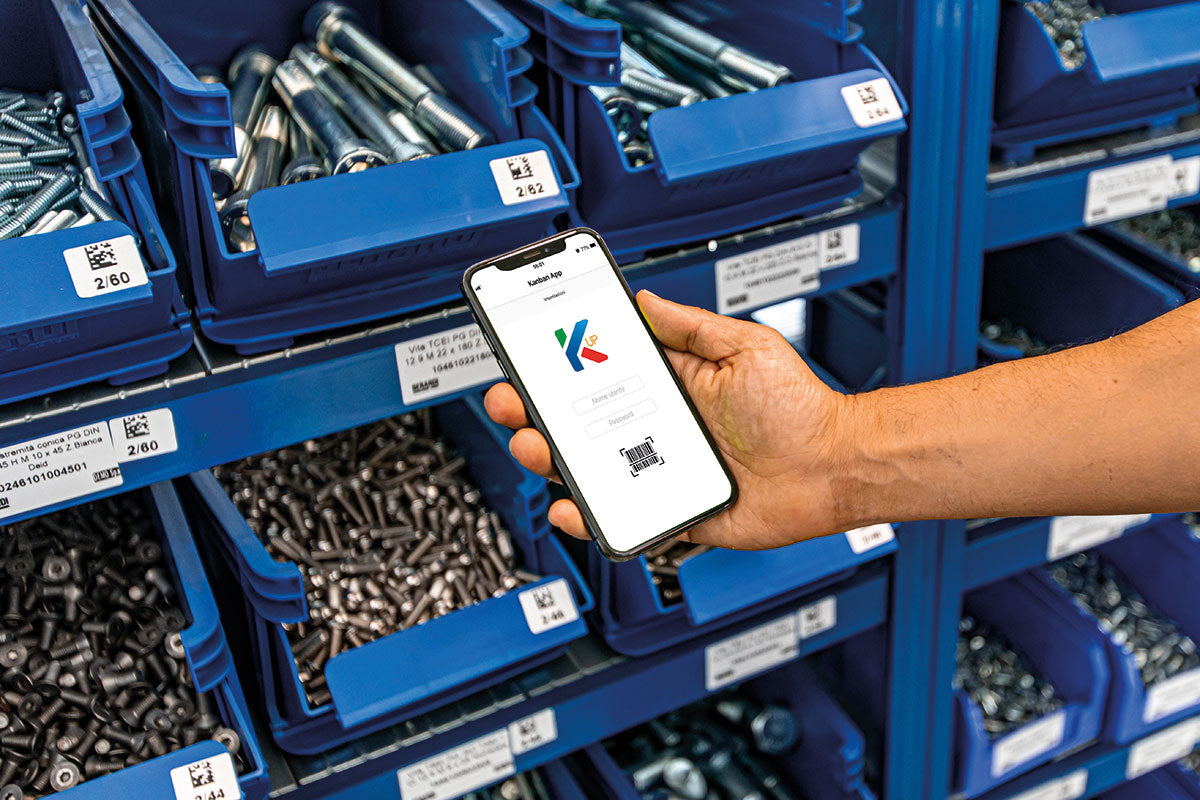
KanbanUp
The Simplicity Revolution for Just-in-Time Supplies
In order to further simplify the replenishment of class C items, Berardi Group offers a new tool for detecting and controlling logistics facilities for all its customers who use the integrated logistics system: KanbanUp . What is it? KanbanUp is the easy-to-use smartphone application for loading your orders at maximum speed.
Deposits 2.0
13 Depots in Italy: from Milan to Bari, from Treviso to Caserta
The management of such a complex and widespread organization is supported by software and hardware that together create an effective hi-tech system active in all warehouses . We are thus able to quickly satisfy the specific requests of the most demanding customer in terms of personalized labeling, real-time sharing of information and management of Kanban and KanbanUp services. You can count on a widespread network of branches throughout Italy , in strategic positions, and ready to guarantee immediate solutions to your emergencies and eliminate the unpleasant consequences of a line stoppage . The Berardi Group branches are in Lombardy in Milan and Brescia , in Veneto in Treviso and Padua , in Emilia-Romagna in Reggio Emilia , Anzola Emilia , Castel San Pietro Terme and Rimini , in Tuscany in Chiesina Uzzanese , in Marche in Ancona , in Lazio in Frosinone , in Puglia in Bari , in Campania in Caserta , all equipped with warehouses containing thousands of items in stock. All the warehouses mentioned are connected in real time with the semi-automated central warehouse of over 10,000 m2 at the Castel Guelfo (BO) headquarters thanks to the support of a dedicated technological system that manages the availability and rapid dispatch of over 50,000 items ready for delivery .
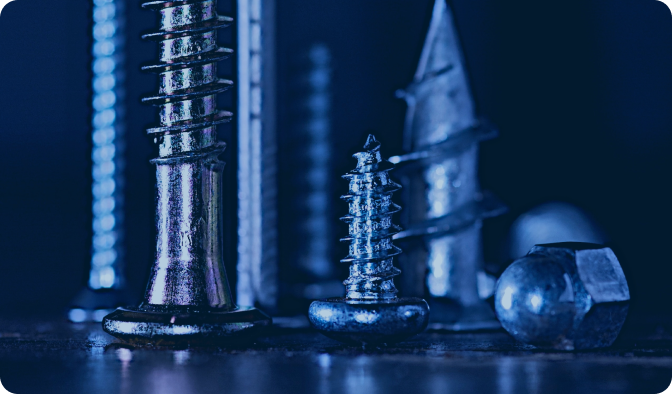
Would you like more information?
Discover how Berardi Bullonerie can improve your work. Request an evaluation (without obligation) and a specific solution for you.